Che impatto hanno la purezza del gas di saldatura e la purezza del gas di taglio?
Air Liquide chiarisce l'importanza della purezza del gas nel processo di saldatura e taglio e la qualità della saldatura. In base al metallo da saldare e al procedimento usato, il grado di purezza del gas influirà sulla velocità della saldatura, sulla finitura del cordone e soprattutto sulla porosità. I vari tipi d'impurità che impattano la superficie generano una serie di difetti e problemi.
Lettura: 4 min
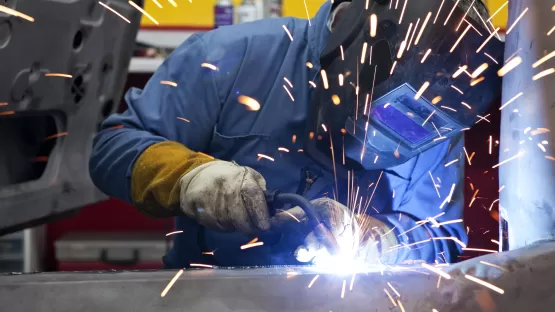
Il gas di saldatura principalmente usato - nel procedimento ad arco elettrico, plasma, laser, TIG, MIG e MAG - è l’Argon; è il gas di base usato per la produzione di metalli.
È bene notare che i livelli d'impurità dell'argon devono essere considerati alla luce del metallo di base e del procedimento per cui si opta. In tal senso l'azoto è estremamente dannoso per l'acciaio ma può essere relativamente neutro per acciai inossidabili austenitici, o addirittura favorevole se usato con acciai duplex, ad esempio. I livelli accettabili d'impurità sono indicati negli standard di saldatura, ma è bene notare che è meglio considerarli in base all'applicazione finale.
L'ossigeno (aria) e l'azoto sono due fra le principali impurità che scaturiscono solitamente dall'Argon, e che hanno effetti negativi quando viene usato questo gas di saldatura nella maggior parte dei procedimenti. Ecco perché Air Liquide vi aiuterà a capire quali sono i livelli di purezza dei gas (puri o miscele) usati a livello industriale per saldare i materiali principali.
Acciaio al carbonio
L'acciaio al carbonio è un materiale che non sopporta l'azoto. L'azoto atomico è infatti solubile nell'acciaio liquido. Non è però solubile nell'acciaio solido. Qualora fosse presente azoto nell'acciaio al carbonio, si formeranno delle bolle durante il processo di solidificazione e di conseguenza il materiale diventerà poroso. Tale fenomeno impatta direttamente la qualità dei pezzi prodotti.
Le condizioni di presenza dei principali agenti inquinanti sono determinate dalla norma EN ISO 14 175. La norma di cui sopra impone che siano presenti meno di 1.000 ppm di azoto. Per quanto riguarda operazioni più esigenti, Air Liquide ritiene tuttavia che tale limite superiore possa influire negativamente sulle proprietà meccaniche. I gas puri o le miscele di gas Air Liquide della linea ARCAL™ contengono infatti nella stragrande maggioranza dei casi meno di 200 ppm di azoto per poter ottenere i migliori risultati.
L'ossigeno (altro componente dell'aria) può essere usato a basse concentrazioni quando bisogna effettuare saldature industriali dell'acciaio. Tuttavia, il tenore di questo componente dev'essere controllato e padroneggiato attentamente per ottimizzare la maneggevolezza, ad esempio in base alla velocità di avanzamento.
L'acqua (H20) si dissocia in prossimità dell'arco sotto forma d'idrogeno e ossigeno. Vi sono forti possibilità che l'idrogeno in particolare passi nell'acciaio. Il che impatta direttamente la qualità poiché indebolisce l'acciaio al carbonio a causa di cricche a freddo. Per le operazioni di saldatura la norma EN ISO 14 175 tollera tra i 40 e i 120 ppm di H20. Air Liquide e la sua linea di gas per saldatura ARCAL™ mantengono solitamente 40 ppm come limite superiore.
Hai qualche domanda sulla saldatura industriale?
Acciaio inossidabile austenitico
Quando si saldano parti in acciaio inossidabile austenitico, l'azoto o l'idrogeno non sono un problema a basso tenore. In alcuni casi possono perfino contribuire favorevolmente alla metallurgia (N2) o migliorare i parametri di funzionamento e l'aspetto del cordone (H2).
Nella saldatura MAG dell'acciaio inossidabile, un elemento ossidante è fondamentale per stabilizzare l'arco. L'eccesso di CO2 può tuttavia provocare precipitati di carburo di cromo nella saldatura, che influiranno sulla resistenza alla corrosione dell'assemblaggio. Generalmente quando si salda acciaio inossidabile, non bisognerebbe quindi usare più del 3% di CO2. Un eccesso di ossigeno avrà lo stesso effetto, sarà più ossidante e quindi più aggressivo, fino al fenomeno delle inclusioni gassose o alla formazione di tarli per esempio. Non bisogna quindi superare il 2-3% di ossigeno nell'argon.
Lo sapevate? I diversi acciai consentono di produrre svariati prodotti utili per il mercato mondiale delle analisi e per il settore medico, dove l'inox è apprezzato poiché limita lo sviluppo di microorganismi. Anche il settore chimico sfrutta gli acciai, in particolare gli acciai inossidabili o i duplex, in base alle temperature e al tipo di corrosione riscontrati.
L'alluminio
L'alluminio non sopporta né livelli relativamente alti di azoto, né l'idrogeno, né l'H2O (acqua). Per evitare la formazione di porosità bisogna quindi considerare gas ad alta purezza.
L'alluminio e le sue leghe sono generalmente saldati in un'atmosfera inerte, ad esempio in argon e argon/elio, o anche in elio puro in alcuni casi. Particolare attenzione dev'essere prestata alla preparazione dello strato superficiale prima della saldatura: l'allumina presente superficialmente sugli elementi da trattare può contenere abbastanza umidità da generare porosità anche con un gas contenente pochissime impurità.
Air Liquide è un'azienda leader a livello internazionale nell'ambito dei gas industriali ed è in grado di fornirvi consulenza riguardo al grado di purezza necessario per le vostre esigenze industriali. La maggior parte dei gas Air Liquide, in particolare la linea ARCAL™, supera di gran lunga i requisiti normativi.
Hai qualche domanda sulla saldatura industriale?
Scopri le nostre soluzioni
Hai qualche domanda sulla saldatura industriale? Compila il nostro modulo di contatto.
I nostri esperti risponderanno il prima possibile.Maggiori informazioni
Vuoi saperne di più?
Maggiori Informazioni
- Taglio Laser
- Saldatura al plasma
- Taglio plasma
- Il processo di saldatura MIG/MAG (GMAW)
- I caschi e le maschere da saldatori
- Il processo di ossitaglio degli acciai
- Temperatura di fusione di un metallo
- Generatori di saldatura
- Metallo d'apporto in MIG/MAG
- Processo ad arco sommerso
- Torce di saldatura
- Saldatura a resistenza
- Saldatura TIG / di metalli
- Miscela di gas per la saldatura per fusione
- Difetti di saldatura
- Il metallo d'apporto
- Saldatura ad arco plasma
- Processo di brasatura
- Rame e leghe
- Saldatura industriale
FAQ
- Come si regola l'erogazione del gas durante la saldatura?
- Qual è la differenza tra i processi di saldatura MIG e MAG?
- Come si salda l'acciaio galvanizzato?
- Come si sceglie il gas da usare nella saldatura MIG o MAG?
- Perché bisogna usare il filo animato
- Come si salda l'acciaio al carbonio?
- Come si salda l'alluminio?
- Che impatto hanno la purezza del gas di saldatura e la purezza del gas di taglio?
- Quali sono i difetti di saldatura più comuni?
- Come si salda l'acciaio inossidabile?
- Che differenza c'è tra brasatura e saldatura?
- Come si sceglie il gas da usare nel procedimento TIG o Plasma?
- Come si fa ad evitare un consumo eccessivo di gas di saldatura?
- Come scegliere il gas giusto per la saldatura TIG?