Saldatura “a freddo” e “a stagno” vs. saldatura laser
Il termine "saldatura a freddo" può riferirsi a due tecniche molto diverse tra loro: la saldatura a freddo dei metalli e la saldatura a stagno. Ecco una descrizione di ciascuna, con i materiali utilizzati, i settori industriali, le tipiche applicazioni e un confronto con l'uso della saldatura laser come alternativa.
Lettura: 4 min
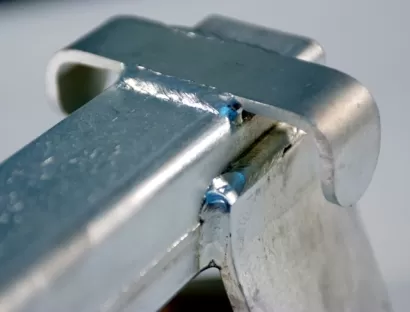
Il termine "saldatura a freddo", in gergo è talvolta associato a due tecniche diverse: l'unione di metalli a bassa temperatura, senza l’utilizzo di fonti di calore (propriamente “saldatura e freddo”) e la saldatura a stagno, comunemente utilizzata in elettronica.
La saldatura a freddo dei metalli utilizza principi chimico-fisici per unire materiali come ad esempio l'alluminio o il rame, ed è comune in settori industriali come l'aerospaziale ed elettronico.
La saldatura a stagno è diffusamente utilizzata e cruciale per l'assemblaggio di circuiti stampati e utilizza leghe a basso punto di fusione per l’unione dei componenti.
La saldatura laser offre vantaggi significativi rispetto alla saldatura a freddo e a stagno in termini di precisione, velocità, robustezza del giunto, compatibilità dei materiali e controllo della zona fusa e della zona termicamente alterata. È la tecnica preferita per applicazioni che richiedono alta precisione, produttività e robustezza, anche se può essere più costosa e richiede attrezzature avanzate rispetto alle altre tecniche.
In entrambi i casi, la saldatura laser offre un'alternativa efficace ai due procedimenti, migliorando la precisione e la produttività, ma con costi e complessità operativa maggiori.
Hai qualche domanda sulla saldatura “a freddo”, “a stagno” o saldatura laser?
Saldatura a Freddo dei Metalli
La saldatura a freddo dei metalli è un processo in cui due superfici metalliche vengono unite senza l'applicazione di calore. Il legame tra le superfici metalliche avviene principalmente grazie alla coesione atomica. Quando due superfici metalliche vengono portate a stretto contatto, se la pressione applicata è sufficientemente elevata e le superfici sono prive di ossidazione e impurità, gli atomi dei due metalli possono interagire direttamente. Questa interazione si verifica a livello atomico, dove le forze di Van der Waals e legami metallici contribuiscono alla formazione del legame.
In condizioni ideali, la distanza tra gli atomi delle due superfici diventa così ridotta che si instaurano forze di coesione sufficienti a tenere unite le superfici senza la necessità di una fusione. È importante notare che la presenza di contaminanti o ossidi può essere causa di difetti e impedire questa coesione, avendo cura che la superficie di contatto pre saldatura sia opportunamente pulita.
Materiali Trattati
- Alluminio e sue leghe
- Rame e sue leghe
- Oro, Argento, Platino (metalli preziosi, usati soprattutto in elettronica e gioielleria)
Settori Industriali e Tipiche Manifatture
- Industria Aerospaziale: Per la produzione di componenti in alluminio e titanio.
- Elettronica: Giunti per cavi e connettori.
- Orologeria e Gioielleria: Per unioni di alta precisione di metalli preziosi.
La saldatura a stagno
La saldatura a stagno è un procedimento largamente utilizzato in elettronica e nella lavorazione di piccoli componenti metallici. Questo metodo utilizza una lega a base di stagno per unire parti metalliche attraverso un processo che implica la fusione del materiale di apporto.
La lega per saldatura è solitamente a base stagno, rame e argento, tali leghe fondono a temperature di 200°C circa.
Al fine di evitare l’ossidazione delle superfici metalliche viene utilizzato un flussante che permette di eliminare anche eventuali ossidi già presenti, facilitando così la bagnatura del metallo da parte della lega fusa.
E’ una fase essenziale la pulizia delle superfici da saldare. Viene utilizzato alcool isopropilico o altro solvente non conduttivo per rimuovere ossidi, grasso o altre contaminazioni fonti di potenziali difetti.
Il riscaldamento si effettua con un saldatore alimentato a corrente elettrica che presenta una punta che viene portata a temperature di circa 300-400°C, a seconda del tipo di lega utilizzata. La punta del saldatore viene portata a contatto con le superfici metalliche e mantenuta in posizione per qualche secondo per riscaldare uniformemente l’area da saldare. Una volta che l'area è sufficientemente calda, la lega di saldatura viene applicata. Il filo di stagno si fonde e, grazie al flussante, fluisce uniformemente sulla superficie riscaldata, bagnando il metallo. Una volta che la lega fusa copre l’area desiderata e forma una connessione omogenea tra i componenti metallici, si rimuove il saldatore e si lascia raffreddare la giunzione. Durante il raffreddamento, la lega solidifica, creando una continuità elettrica e meccanica tra le parti.
Durante la saldatura, il metallo di apporto forma un legame metallurgico con le superfici metalliche. Questo legame avviene grazie alla diffusione atomica tra la lega fusa e il metallo base, formando uno strato di composti intermetallici che garantisce la robustezza del giunto.
E’ un processo relativamente semplice e rapido, eccellente per giunzioni elettriche e non richiede attrezzature complesse o costose.
Di contro, la robustezza meccanica dei giunti saldati a stagno può essere limitata, soprattutto se esposti a vibrazioni o stress meccanici.
La saldatura a stagno è indispensabile nella fabbricazione delle schede elettroniche e relativi accessori, utilizzata per collegare componenti a circuiti stampati, connettori e cablaggi. È anche utilizzata in artigianato per unire piccole parti metalliche, come nella produzione di gioielli o modelli.
La saldatura laser
La saldatura laser è una tecnica avanzata che utilizza un raggio laser per fondere e unire metalli. È ampiamente utilizzata in applicazioni industriali, mediche, aerospaziali e in elettronica di precisione. Rispetto alla saldatura a freddo e alla saldatura a stagno, la saldatura laser permette di avere una elevata precisione e controllo del processo. E’ possibile focalizzare il laser con grande precisione su aree molto piccole, permettendo di ottenere giunti estremamente sottili e precisi, con un controllo eccellente sulla profondità e sull'ampiezza della saldatura. Questo è particolarmente utile in applicazioni dove è necessario lavorare su componenti miniaturizzati o dove la precisione dimensionale è critica.
Il processo laser inoltre è molto rapido, permette una produzione su larga scala con tempi di ciclo ridotti. Il laser può eseguire saldature in frazioni di secondo, rendendolo ideale per applicazioni ad alta velocità, come nell'industria automobilistica o elettronica.
I giunti prodotti sono molto robusti e di alta qualità, con un'eccellente continuità metallurgica. Il raggio laser può penetrare profondamente nel materiale, creando saldature ad alta resistenza anche a carichi elevati e in ambienti severi.
La saldatura laser è anche molto versatile e può essere utilizzata su una vasta gamma di materiali, inclusi metalli di alto punto di fusione, leghe complesse e materiali diversi tra loro (come metalli e ceramiche). Il laser può essere utilizzato per saldare materiali sottilissimi senza danneggiarli.
Sebbene implichi l'applicazione di calore, la zona termicamente alterata può essere ridotta al minimo grazie alla concentrazione termica del raggio laser. Questo è fondamentale quando si lavora con materiali che sono sensibili alle alte temperature o che non devono subire modifiche nelle loro proprietà meccaniche.
Grazie alla sua precisione, velocità e capacità di saldare materiali diversi, è spesso utilizzata in applicazioni specialistiche come la produzione di componenti aerospaziali, microelettronica, dispositivi medicali, e strutture complesse in ingegneria di precisione.
La saldatura laser offre indubbi vantaggi rispetto alle altre tecniche, tuttavia va valutato, rispetto alla propria produzione, l’aspetto relativo agli investimenti e ai costi operativi (gas, energia, manodopera) e di manutenzione. La saldatura laser inoltre richiede una maggiore attenzione (e relativi oneri) alla valutazione dei rischi connessi all’attività e all’implementazione di tutte le misure di prevenzione e protezione per la sicurezza degli operatori.
Hai qualche domanda sulla saldatura “a freddo”, “a stagno” o saldatura laser?
Hai qualche domanda sulla saldatura “a freddo”, “a stagno” o saldatura laser? Compila il nostro modulo di contatto.
I nostri esperti risponderanno il prima possibile.Vuoi saperne di più?
Maggiori Informazioni
- Saldatura Laser
- Saldatura TIG dei metalli
- Come si salda l'alluminio?
- Qual è la differenza tra i processi di saldatura MIG e MAG?
- Saldatura ad arco elettrico
- Che differenza c'è tra brasatura e saldatura?
- Quali sono i principali tipi di saldatura a flusso di gas?
- Saldatura del rame con procedimenti a gas
- Come saldare l'acciaio con tecnica laser?
- Quanti tipi di laser per saldatura esistono e quali sono le differenze?
- Differenti tipi di sorgenti laser per saldatura
- Qual è la differenza tra saldatura a punti e saldatura laser?
- Saldatura laser manuale: Analisi dei rischi e misure di sicurezza
- Come realizzare una microsaldatura laser?
- Perché la velocità è importante nella saldatura laser?
- Vantaggi della saldatura laser
- Campi di applicazione della saldatura laser
- Controllo di qualità nella saldatura
- Cos'è la saldatura fine (thin welding, fine welding)?
- Saldatura a Conduzione Termica
- Saldatura laser automatizzata
- Saldatura di Profondità (Keyhole Welding)
- Utilizzo dei cobot nella saldatura
- Guida alla saldatura laser delle leghe: tipi, specificità e precauzioni
- Quali sono le principali sorgenti laser, i loro vantaggi e svantaggi?
- La saldatura solida
- Impianti di saldatura laser
- Saldatura Laser Manuale
- Area di saldatura: aspetti meccanici e metallurgici
- Macchina di saldatura laser
- Qualifiche di procedimento WPS saldatura laser
- FLAMAL™, la gamma di gas Air Liquide per tutte le operazioni alla fiamma
- Il taglio plasma
- Come si sceglie il gas da usare nel procedimento TIG o Plasma?
- Il processo di saldatura MIG/MAG (GMAW)
- Saldatura autogena o ossiacetilenica